Несмотря на конструктивную простоту, технических характеристик тормозных дисков вы особо не найдете. Поэтому за базовую информацию принимается то, что практически все компоненты изготовлены из серого чугуна, с пластинчатым (иногда вермикулярным) содержанием графита. А это значит, что все чугунные диски подвержены одним и тем же рискам, а следовательно, реагировать на нагрузки будут примерно одинаково.
Но кроме базовых данных, за последние 10-15 лет, производители разработали и внедрили ряд опций, улучшающих свойства тормозных дисков. Однако, общедоступные источники не приводят результатов опытных исследований этих доработок, почему и возникает масса, так скажем, разночтений.
На базе доступных нам внутренних технических исследований разных производителей, мы подготовили обзор основных доработок и их эффективности.
1. Карта вентиляционных каналов.
Вентилируемые тормозные диски, как известно, имеют внутренние полости между двумя пластинами, для дополнительного охлаждения конструкции. Классическая модель вентиляционных каналов — это ребра, лучеобразным образом направленные от ступичной части к внешнему краю. Модернизация системы охлаждения реализована через изменение геометрии внутренних перегородок. Вся эволюция апгрейда вентиляционных каналов прошла три этапа: лучеобразные ребра, радиально направленные и диффузорно-конфузорная система.
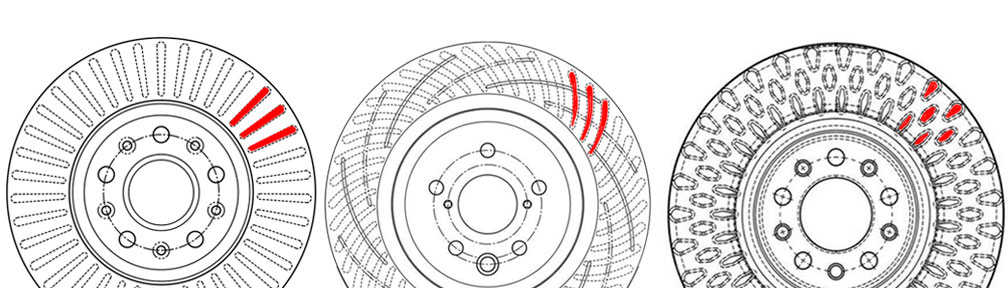
В версии с радиальными перегородками, за счет увеличения длины ребер, происходит ускорение воздушного потока и связанный с ним рост теплоотдачи. Более эффективная новация — система перемычек диффузорно-конфузорного типа (ребра расположены чередующимися «островками»), благодаря турбулизации воздушного потока, позволяет ускорить его до 60% (в сравнении с классической моделью).
2. Перфорированный диск
Содержание модификации заключается в нанесенных по всей поверхности рабочего полотна сквозных отверстий, которые призваны способствовать интенсификации охлаждения рабочего полотна. Вторичная функция перфорированного тормозного диска — дегазация (отвод газов, неизбежно образующиеся в точке контакта фрикционной пары «диск-колодка»). Базовый диаметр перфорации составляет 3,5-3,9 мм, что является оптимальным с точки зрения «эффективность охлаждения-ослабление конструкции диска». Логика разработки заключается в увеличении площади поверхности трения, без изменения размеров диска. В частности, количество тепла, отданного в атмосферу (рассеянного) зависит от площади тела. Сверление сквозных отверстий позволяет:
а) увеличить площадь омываемой поверхности;
б) ускорить отвод тепла за счет перенаправления во внутренние вентиляционные каналы.
В Испанском Институте в Куала-Лумпур провели сравнительное исследование, целью которого было выявить практическое влияние внутренней вентиляции, а также сквозных отверстий на интенсивность охлаждения перфорированного тормозного диска. Были созданы разнозначные нагрузки, по итогам которых осуществлены замеры температуры.
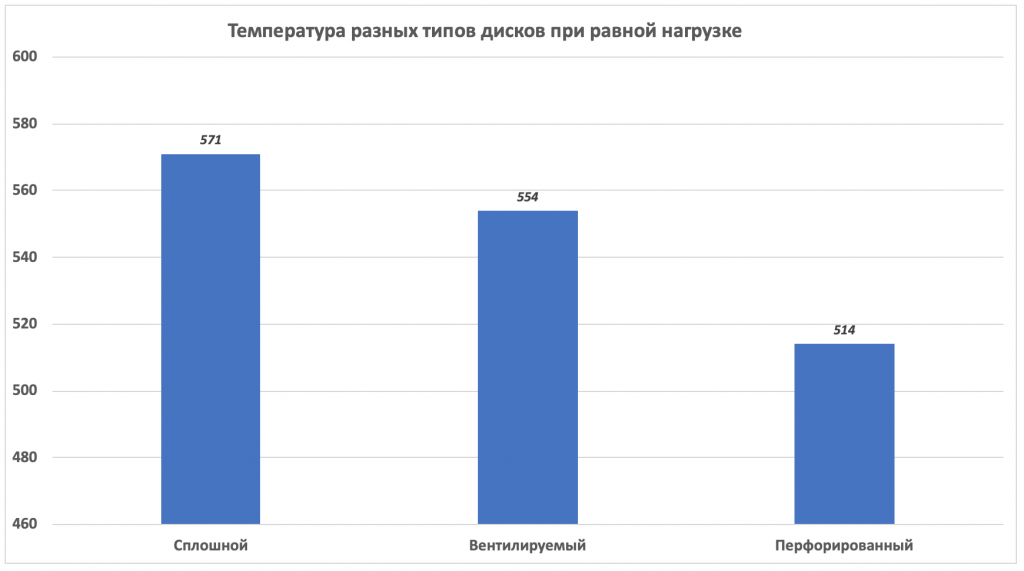
То есть, в момент нагрева перфорация прохладнее сплошного аналога на 10%. Однако, более важным критерием оценки есть интенсивность последующего охлаждения. И здесь перевес в пользу сквозной перфорации еще более уверенный.
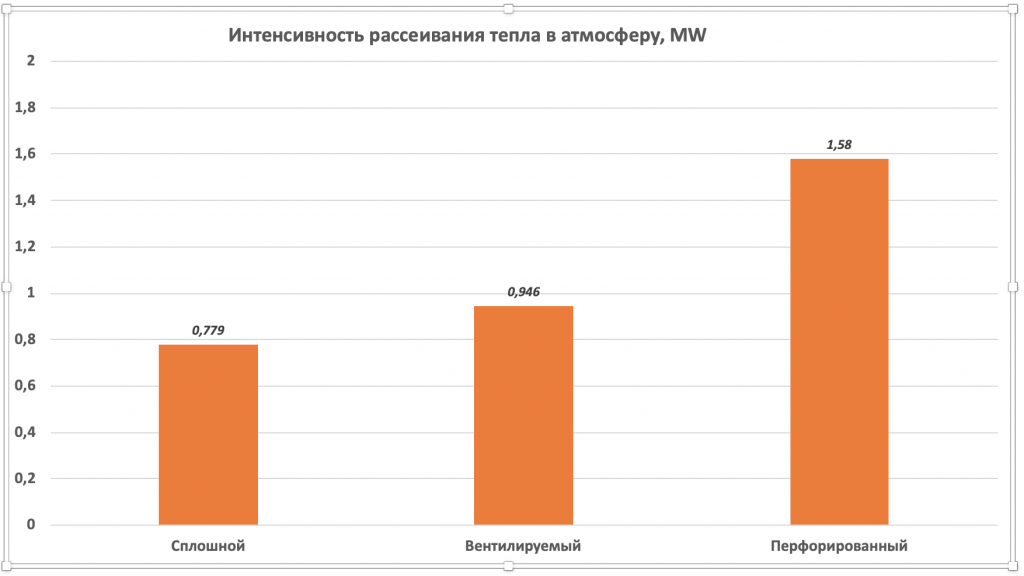
Таким образом, с точки зрения теплоотдачи (скорости охлаждения), перфорированный тормозной диск на 66% эффективнее, чем вентилируемый, а вентилируемый, в свою очередь, на 22% быстрее охлаждается, чем сплошной.
Перекрестная статистика. Согласно внутренних исследований, проведенных производителем Power Stop, при равных условиях нагрузок и физических параметрах, разница в температуре нагрева достигает 180 °С, перфорированного тормозного диска в сравнении с гладким.
3. Радиальные насечки (слотирование)
Технология нарезки радиально расположенных дренажных канавок на поверхности диска. Рисунок насечек встречается различный, но эффективным считается расположение канавок радиально направленных, от ступичной части к внешнему краю заготовки. Ключевые задачи технологии — отвод отработанных газов, воды и пыли от «пятна» контакта «диск-колодка» и очищение (реновация) рабочей поверхности фрикционной накладки. Вторичная задача тормозного диска с насечкой — повышение динамического коэффициента трения пары.
Несмотря на расхожее мнение, износ тормозных колодок, скомбинированных со слотированными дисками, ускоряется не более чем 3-5% (в сравнении с гладкими компонентами).
4. Двусоставной тормозной диск
Одно из эффективных и многофункциональных решений. Суть технологии в разделении цельнолитой конструкции на две составляющих — ступичной части (как правило, алюминиевой), которая через болтовые крепления (бобинсы), сочетается с чугунным рабочим полотном.
Ключевые функции: снижение риска коробления рабочего полотна диска, снижение неподрессоренной массы автомобиля, а также задача экранирования суппорта и ступицы от передачи тепла. Одной из отличительных особенностей такого типа дисков является т.н. «плавающее» крепление ступичной части и полотна, которое позволяет рабочей части расширяться без конической деформации.
Современные двусоставные тормозные диски, при сохранении штатных физических размеров, могут иметь массу на 20-25% меньшую, чем стоковые запчасти. Одной из последних разработок является технология облегчения диска, с одновременной интенсификацией теплоотдачи: применены радиальные ребра внутренних каналов, сквозная перфорация, ускорен захват набегающих потоков. Такое решение позволяет компенсировать собственную теплоемкость чугунной болванки без потери способности теплообмена.
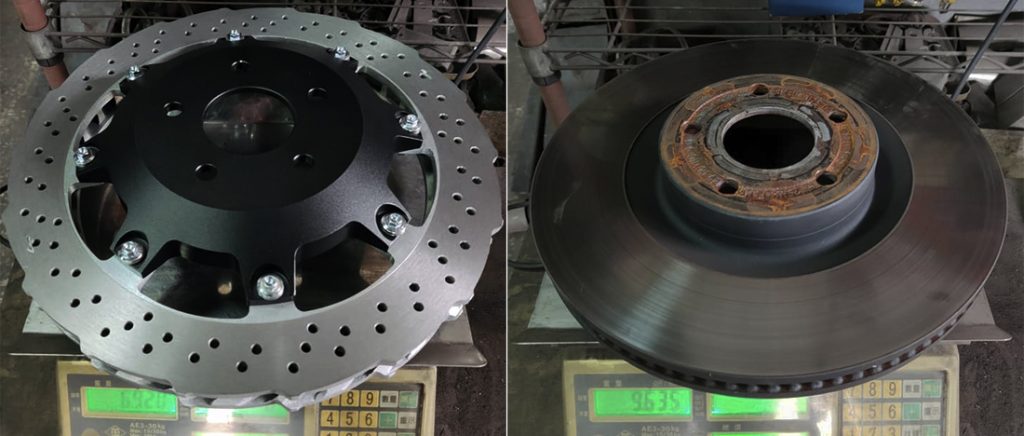
Важно отметить, что вышеперечисленные технические опции не нарушают действующий в ЕС регламент ECE R90, и являются допустимыми для установки на серийные автомобили.
5. Карбон-керамический (композитный) диск
Композит — это технология смешения и последующей обработки различных компонентов таким образом, что новосозданный материал по свойствам превосходит суммарные характеристики использованных ингредиентов. Изготавливаются такие диски из карборунда (карбида кремния). Ключевыми преимуществами фрикционных составов на основе углеродной матрицы являются высокий коэффициент трения, теплостойкость углеродной основы (свыше 1000 °С), размерно-температурная стабильность в различных режимах. Диск производится на основе композитор с карбидкремниевой матрицей, армированной углеродными волокнами (Cf/SiC), эффективно нивелирующими возникающие в материале напряжения. Главными достоинствами фрикционных композитов на основе углеродной матрицы являются высокий коэффициент трения, теплостойкость углеродной базы (до 1000 °С), размерно-температурная стабильность
При этом есть и недостатки. Несмотря на высокую термическую стойкость, в зоне свыше 450 С износ карбон-керамических дисков значительно ускоряется. Поэтому ресурс таких компонентов будет значительно зависим от условий эксплуатации. Кроме того, диски из карбон-керамического композита хрупки. Цена такого изделия может в 15-20 раз превышать стоимость чугунного аналога на данную модель авто.
Ресурс такого диска, в среднем, составляет 250-350 тысяч километров. Он практически лишен риска традиционной для чугуна деформации, при этом имеет массу на 40-60% меньшую, чем металлический аналог.